Indonesia
Breadcrumb navigation
Predictive Detector(SIAT)
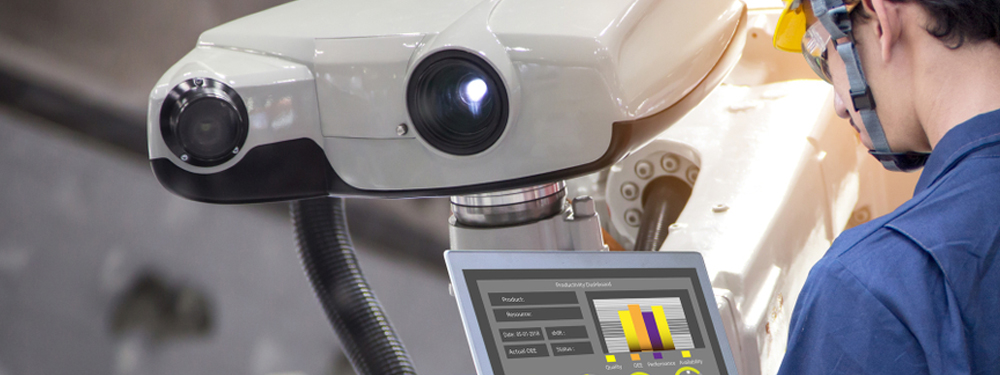
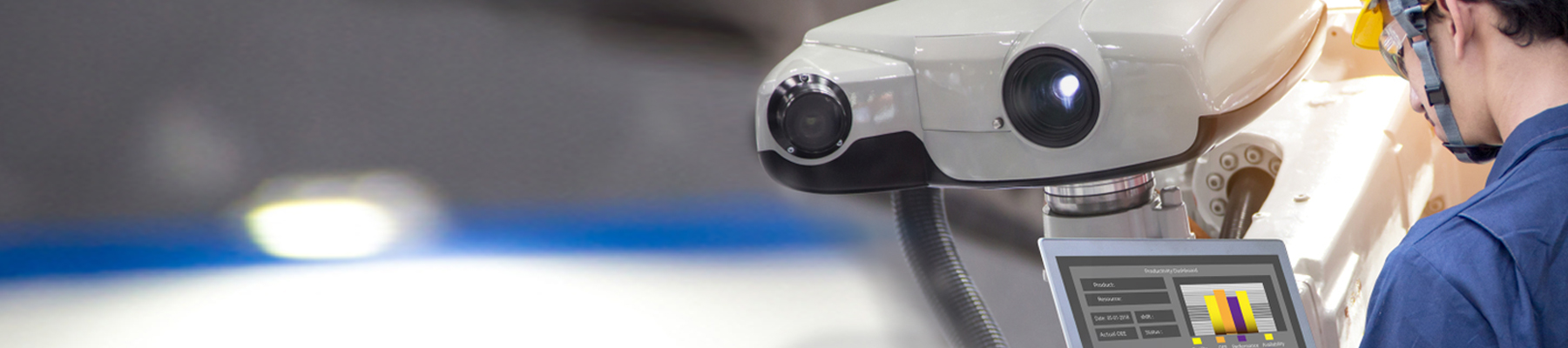
Discover "unusual", prevent accident and abnormalities
System Invariant Analysis Technology (“SIAT”), is part of NEC's cutting-edge portfolio of AI technologies, "NEC the WISE", is being used to automatically learn and model the behavior of systems based on data gathered from a large number of sensors installed in large-scale, complex systems. This provides visualization of systems and how they operate, in addition to enabling systems to operate safely and efficiently by proactively detecting errors using analytical models. NEC has already installed approximately 100 such systems internationally.
In recent years, with the acceleration of digitization and the spread of IoT, the safety, efficiency, maintenance and product quality of systems are being visualized and analyzed based on data collected from a large number of sensors installed in various locations, such as plant systems, manufacturing lines and factories.
However, it is necessary to systemize data collection, storage, monitoring, analysis and other processes in order to utilize sensor data. Moreover, unique know-how, such as knowledge about IoT systems and data analysis, is required to construct such a system, making it difficult for customers to construct by themselves.
In addition, especially in the manufacturing industry, work processes are often based on the expertise of each plant or individual. Therefore, the loss of know-how due to the retirement of skilled personnel and lack of staff poses a serious challenge.
In order to solve these issues, NEC have enhanced their products to enable greater visualization and analysis of sensor data that is not only transforms machine operation from preventive to predictive with digitalization but going forward can be modified as prescriptive maintenance for smart, efficient and cost effectivity.
With NEC’s industrial AI technology with anomaly modelling, we can directly recognize the root cause of the machine anomaly that is different from the normal status or condition. Also, can send early detection that is able to monitor and give feedback for maintenance suggestion.
For mass production quality control, we can develop zero defect product by maximizing sensor signal on every machine that can be integrated into the system production line in real time. With this technology, quality control and productivity can be increased significantly by reducing number of defect products.
Contact Us